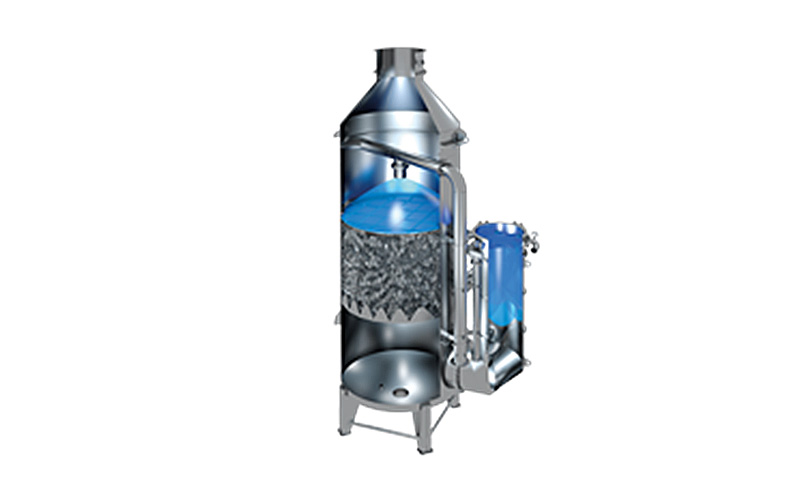
Outline of Scrubber
The SAACKE U-Type multi stream exhaust gas cleaning system (EGCS) fits for both, retrofits and newbuildings and can be configured for open loop or hybrid/closed loop execution.
Exhaust gases of main engine, auxiliary engines and boilers are gathered in a manifold and routed to the “quench”, the first spray nozzle layer, where the exhaust gas temperature if lowed to less than 100°C and where the majority of dust and ashes is captured. From here the exhaust gases flow upwards through the main tower body passing a packed bed reactor which is sprinkled with sea* water from the top. In this second stage the desulfurization process is completed. The result is more than 99 percent sulfur separation. In other words: a SAACKE EGCS always reliably achieves a SO2/CO2 ratio of less than 4,3 which equals the use of MDO with less than 0,1% S and can therefor also be used in ECA zones.
When entering zero discharge zones, a SAACKE Hybrid Scrubber can be switched from open- to close loop operation by just pressing a single button. In this mode the alkalinity, necessary to run the desulfurization process, is provided by a NaOH dosing unit whereas a process* water pump delivers the wash water to the quench and the main spray layer on the top of the tower. The process water quality is monitored by a dedicated water analytics and is maintained by means of a centrifuge separator. Pumps are frequency controlled, depending on the actual exhaust gas load. Thus reduces the electrical demand to a minimum.
In 2014 SAACKE successfully conducted and commissioned a hybrid EGCS installation on MT Levarna, which was the first scrubber installation approved by DNV-GL
Since that time many reliably running references have been added.
The latest development of SAACKE is the so called “Fleet Cockpit”.
On a first glance, all ships of the shipping company equipped with a SAACKE plant and connected to the system, are displayed on a map with the nautical position and a "traffic light status".
In case of anomalies, the operator, with just one more kick, can remotely access the HMI of the plant, and view all load conditions, alarms and operating states (damper positions, pups power demand, etc.) in real time.
So the alarm history can easily be analyzed, the “drift” of measured values and thus the necessity of calibrating sensors can be checked, orders for consumables can be placed in due time, services (if necessary at all) can perfectly be prepared and can be carried out at the most convenient occasion and last but not least this system delivers best arguments in case of disputes with port state controls.
Electrode
Sea chest
Reaction tank
Shaft Grounding Assy
Impressed Current Cathodic Protection(ICCP)
Boiler
Burner
GCU
Tank Cleaning (for Ship)
Tank Cleaning (for Industries)
Anti-pirate water cannon
SCANVENT
ScanFinder-B
Incinerator
Ejector
FuelOpt
Fleet Analytics